In May 2013, Ford Australia announced it would close its Australian plants by October 2016. A similar announcement from Holden was to follow, which put shock waves through the Australian automotive industry. With such massive change facing the industry, it’s timely to reflect on a cornerstone of the industry, which in itself has seen massive change; the assembly line.
Henry Ford will always be associated with the assembly line, and although he didn’t invent it, he helped sponsor its development so he could mass produce his famous Model T, which in turn revolutionized the world. Before the Model T, cars were made individually by hand. This was prohibitively expensive for all but the very wealthy. Ford’s assembly line changed all that because the cost of production dropped dramatically.
The very first Holden to roll off an assembly line in Australia was the FX at Fishermen's Bend on 29 November 1948. For the time, it was as cutting edge as you get but more importantly, it was affordable. At £733, it still meant the average worker would take a whopping 94 weeks to save up for one, however it was now achievable and this was all down to the assembly line.
In 1948, approximately ten cars per day would roll off the line at Fishermen’s Bend. During the 1950s, the industry as a whole was producing approximately 160 cars per day. Fast forward to the 1970s and thanks to technology coming along in leaps and bounds, that figure got as high as 1300!
Whilst technology, due in no small part to computerization has helped increase production, the actual tooling used in the assembly line, the moulds and presses that actually make the parts and panels for the cars we drive, still need to physically do their job. Understandably, these are very expensive pieces of equipment. The tooling required on an assembly line to press out a simple bumper bar will cost $200k plus. Multiply that cost by every panel on every model and we are talking serious money.
With the industry’s announcement that it’s about to shut up shop, one might think it will be a sad day for us the car enthusiasts. Surely if the assembly line stops, the tooling gets put in moth balls and will last person to leave please turn off the lights? Well, not quite. This is where Rare Spares comes to the rescue with its line of Holden and Ford Restoration Parts (HRP and FRP), a line of parts, where products are built as close to the original specifications as possible and comprise the use of genuine Holden and Ford drawings and original Holden and Ford tooling where available. Rare Spares has acquired as much of the original tooling as possible to provide its customers with parts that are as close as possible to what rolled off the original assembly line. The industry’s closure will be the end of an era and a sad day, however Rare Spares will continue to keep the restoration market alive with a continuing growth of parts incorporating the HRP and FRP range.
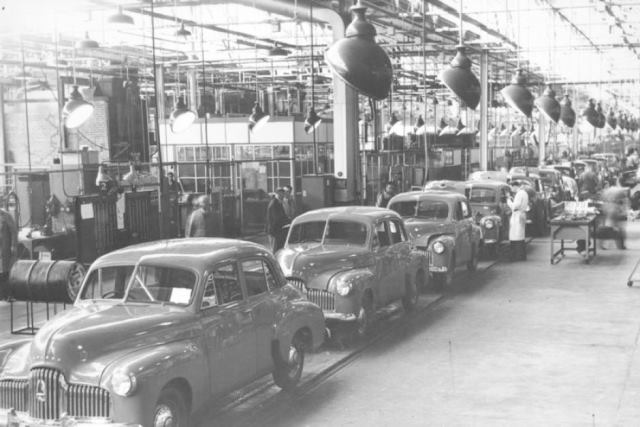